Understanding the Significance of Plastic Mould Tooling in Modern Manufacturing
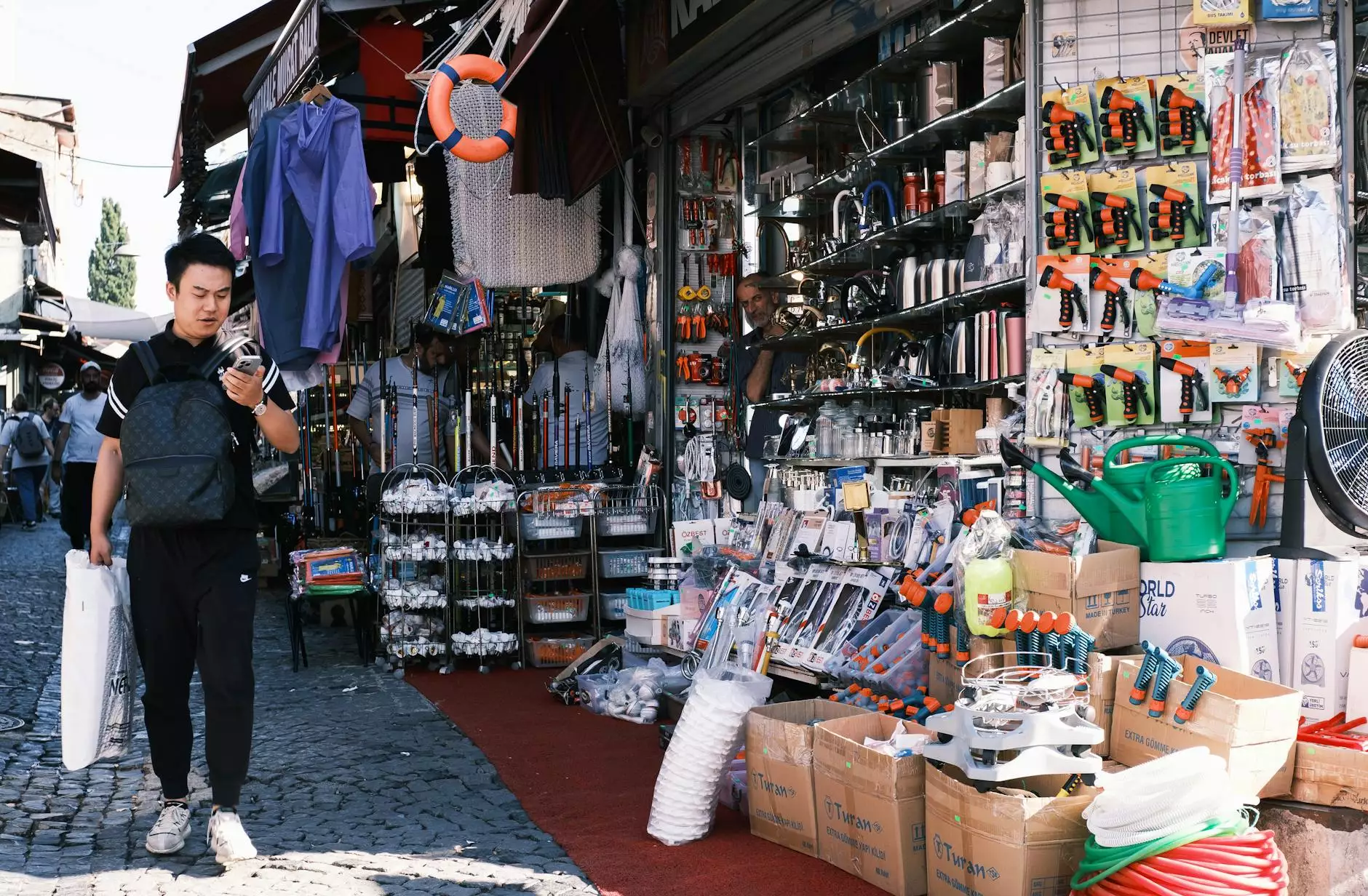
The world of manufacturing is intricate and continually evolving. At the heart of many successful manufacturing processes lies plastic mould tooling, a crucial component that enables the production of plastic parts with precision and efficiency. This article delves deep into the realm of plastic mould tooling, exploring its significance, processes, advantages, and applications across various industries, especially within the context of metal fabricators.
What is Plastic Mould Tooling?
Plastic mould tooling refers to the manufacturing process of creating custom tools and molds used for producing plastic parts. These molds are designed to shape molten plastic into specific geometries, allowing for mass production of identical components. The importance of precision in the design and manufacturing of these tools cannot be overstated, as it directly affects the quality, durability, and performance of the plastic parts produced.
The Components of Plastic Mould Tooling
At its core, the plastic mould tooling process involves several essential components:
- Mold Base: The foundation of the mould, where the cavity and core are mounted. It provides strength and stability.
- Cavities and Cores: The cavity is the part of the mold that shapes the exterior of the product, while the core shapes the interior.
- Cooling Channels: Systems within the mold that help maintain a consistent temperature during the injection process, ensuring even cooling of the part.
- Heating Elements: In some cases, molds are equipped with heating elements to facilitate specific plastic materials that require elevated temperatures.
- Ejection System: Mechanism used to remove the finished part from the mold after the plastic has cooled and solidified.
The Process of Plastic Mould Tooling
The plastic mould tooling process typically involves several key steps:
1. Design and Prototyping
The journey begins with creating a design for the product to be manufactured. Advanced CAD (Computer-Aided Design) software is often employed to create 3D models of both the part and the mold. Prototyping techniques, such as 3D printing, may also be used for validation prior to mold fabrication.
2. Mold Fabrication
Once the design is approved, the next phase is mold fabrication, which involves machining the mold components from high-grade steel or aluminum. Advanced CNC (Computer Numerical Control) machines ensure that the molds are created with utmost precision.
3. Mold Testing
After fabrication, the mold undergoes rigorous testing to ensure that it performs as expected. This includes checking the cooling channels and ensuring proper ejection of parts.
4. Mass Production
Once validated, the mold is ready for mass production. Plastic pellets are heated to a specific temperature, then injected into the mold under high pressure. After a cooling period, the mold opens, and the finished parts are ejected.
Applications of Plastic Mould Tooling
Plastic mould tooling is utilized across numerous industries due to its versatility and efficiency. Here are some notable applications:
1. Automotive Industry
The automotive sector heavily relies on plastic mould tooling for creating various components, such as dashboards, interior panels, and exterior trim. The lightweight nature of plastic parts contributes to fuel efficiency and overall vehicle performance.
2. Consumer Electronics
From smartphones to home appliances, the consumer electronics industry benefits from the precision and aesthetic versatility of plastic parts created through mould tooling.
3. Medical Devices
Medical products often require stringent standards for quality and hygiene. Plastic mould tooling allows manufacturers to produce sterile, precise components for devices such as syringes, vials, and surgical tools.
4. Packaging
The packaging industry uses plastic mould tooling to create a vast array of containers, lids, and other packaging solutions that are both functional and visually appealing.
The Advantages of Plastic Mould Tooling
The utilization of plastic mould tooling in manufacturing offers several significant advantages:
1. Cost-Efficiency
Once the initial investment in tooling is made, the cost of producing each part is significantly reduced, especially when manufacturing in bulk. This makes it highly economical for large-scale production.
2. Design Flexibility
Mould tooling allows for complex designs and intricate details that may be challenging to produce through other manufacturing methods. This flexibility leads to innovative product designs.
3. High Level of Precision
With advancements in technology, modern plastic mould tooling can deliver remarkable precision and consistency, resulting in parts that meet stringent specifications and standards.
4. Durability and Longevity
High-quality molds built from robust materials can endure significant cycle counts, leading to long-lasting tools that minimize replacement costs over time.
Challenges in Plastic Mould Tooling
While plastic mould tooling offers many benefits, it is not without its challenges:
1. Initial Investment
The upfront costs associated with designing and fabricating molds can be steep. However, this cost is typically offset by the long-term savings gained from mass production.
2. Maintenance and Repair
Regular maintenance of molds is crucial for ensuring consistent quality. Over time, molds can wear out and require repairs, which should be planned for financial purposes.
3. Material Limitations
Not all plastics mold well. Manufacturers must select the appropriate type of plastic depending on the application and part requirements, which can complicate the design process.
Future of Plastic Mould Tooling
The future of plastic mould tooling looks promising as technology advances. Some trends that are shaping the industry include:
1. Automation and Smart Manufacturing
Automation is making mould manufacturing faster and more efficient. Smart factory concepts leverage data analytics and IoT (Internet of Things) to optimize processes.
2. Sustainable Materials
With increasing awareness of environmental issues, the demand for sustainable materials is rising. Manufacturers are exploring bioplastics and recyclable materials to reduce environmental impact.
3. Additive Manufacturing Integration
Integrating 3D printing technologies with traditional mould tooling processes can enhance flexibility and allow for rapid prototyping, reducing time to market for new products.
In conclusion, plastic mould tooling is a cornerstone of modern manufacturing, enabling various industries to produce high-quality plastic parts efficiently and cost-effectively. As technology evolves, the potential for innovation and improvement within this field continues to grow, ensuring that it remains a vital component of manufacturing strategies for years to come. For metal fabricators and manufacturers alike, understanding and leveraging this technology can lead to significant competitive advantages in the marketplace.
For more information on how plastic mould tooling can revolutionize your manufacturing processes, visit deepmould.net.